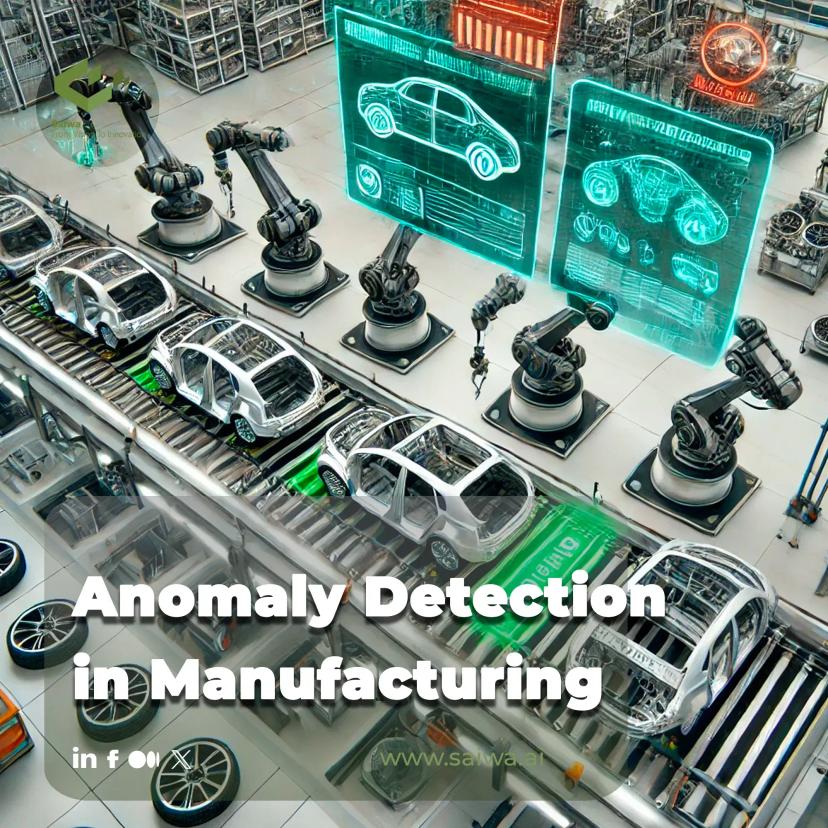
Anomaly Detection in Manufacturing
The manufacturing industry is undergoing a rapid transformation driven by automation, data analytics, and the Industrial Internet of Things (IIoT). In this increasingly complex and data-rich environment, ensuring product quality, optimizing productivity, and maintaining operational safety are paramount.
Anomaly detection, a powerful technique leveraging artificial intelligence (AI) and machine learning (ML), is emerging as a critical tool for achieving these objectives. By identifying unusual patterns and deviations from expected behavior, anomaly detection enables manufacturers to proactively address potential problems, prevent costly failures, and enhance overall operational efficiency.
Saiwa is an AI-driven company that provides AI-as-a-Service (AIaaS) and machine learning solutions through its Fraime platform. Fraime provides a wide range of services, including detection, deep learning, annotation, and image processing. Among these, anomaly detection stands out, especially in the context of surface defect detection, which is a critical aspect of quality control in manufacturing. By leveraging AI to identify even the most subtle surface irregularities, Fraime's anomaly detection services improve operational efficiency, reduce waste, and ensure product quality, making it a valuable tool for manufacturers seeking to optimize their production lines.
This article provides a comprehensive overview of anomaly detection in manufacturing, exploring its principles, applications, benefits, and future trends.
What is an Anomaly?
An anomaly, also known as an outlier, is a data point or observation that deviates significantly from the expected pattern or behavior within a dataset. Anomalies can take various forms, including:
Point Anomalies
Individual data points that are significantly different from the rest of the data. These anomalies stand out as isolated occurrences and are often easily detectable using statistical methods. Examples include a sudden spike in temperature readings from a sensor or a single product with significantly different dimensions than others in a batch.
Contextual Anomalies
Data points that are anomalous within a specific context, such as a particular time period or operating condition. These anomalies are only considered unusual when the surrounding context is taken into account. For instance, a temperature reading that is normal during the day might be considered anomalous if it occurs at night when the equipment is supposed to be idle. Similarly, a certain level of vibration might be acceptable at low speeds but anomalous at high speeds.
Collective Anomalies
A group of data points that are anomalous when considered together, even though individual data points may not appear anomalous on their own. These anomalies represent a shift in the overall pattern or behavior of the data. For example, a gradual increase in temperature over time might not be noticeable when looking at individual readings, but when considered collectively, it could indicate a developing problem such as equipment degradation or a slow leak. Identifying collective anomalies often requires analyzing the data over a period of time and looking for trends or patterns.
Anomalies can be indicative of various underlying problems, such as equipment failures, process deviations, or product defects. The ability to detect and interpret anomalies is crucial for maintaining operational efficiency and preventing costly failures.
Types of Anomaly Detection Models in Manufacturing
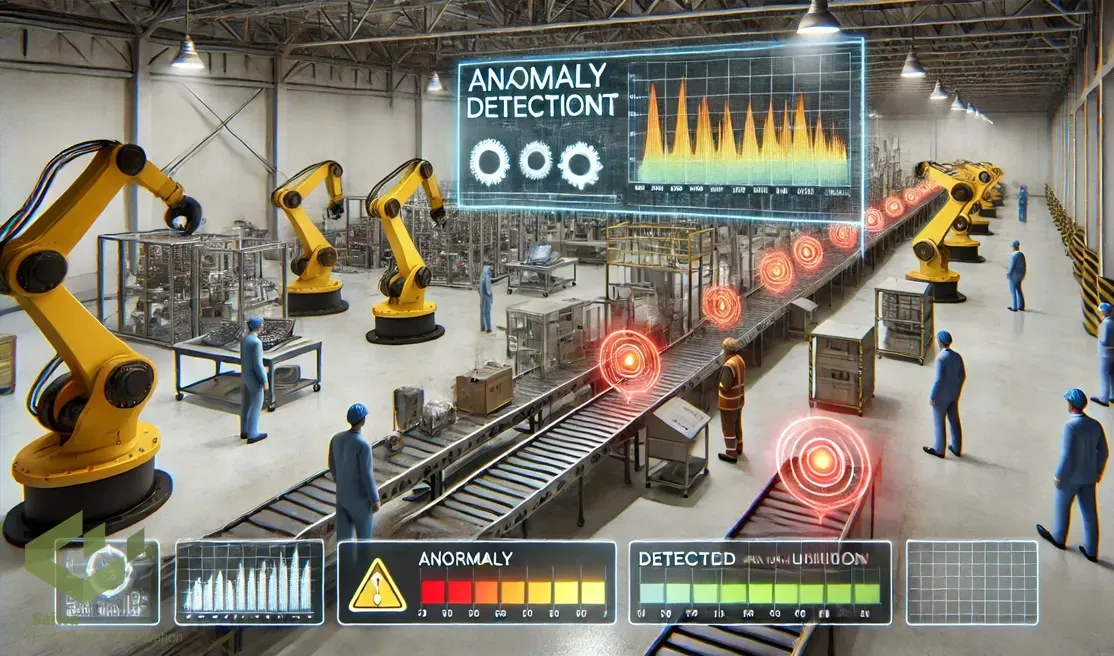
Several types of anomaly detection models are employed in manufacturing, each with its own strengths and weaknesses:
Supervised Anomaly Detection
Supervised anomaly detection models are trained on labeled datasets containing both normal and anomalous examples. The model learns to distinguish between these two classes and can then classify new, unseen data points as either normal or anomalous. Supervised methods are effective when sufficient labeled data is available, but they can be challenging to implement in real-world scenarios where labeled anomaly data is often scarce.
Unsupervised Anomaly Detection
Unsupervised anomaly detection models do not require labeled data. These models learn the underlying patterns and distributions of the normal data and identify data points that deviate significantly from these learned patterns as anomalies. Unsupervised methods are more versatile and applicable in scenarios where labeled data is limited or unavailable. Common unsupervised techniques include clustering, density-based methods, and one-class SVM.
Semi-Supervised Anomaly Detection
Semi-supervised anomaly detection models leverage a combination of labeled and unlabeled data. These models typically learn a model of normal behavior from a labeled dataset of normal examples and then identify deviations from this learned model in unlabeled data as anomalies. Semi-supervised methods can be effective when some labeled data is available but not enough to train a fully supervised model.
Applications of Anomaly Detection in Manufacturing
Anomaly detection finds numerous applications in manufacturing, including:
Product Quality Control
Anomaly detection can be used to identify defects in finished products, ensuring that only high-quality products are shipped to customers. This can be achieved by analyzing various data sources, including images of products captured by vision systems, sensor data from testing equipment measuring dimensions, weight, or other critical parameters, and other relevant data sources like customer feedback or warranty claims.
By automatically detecting anomalies in product characteristics, manufacturers can quickly identify and isolate defective products, preventing them from reaching the customer and minimizing the impact on brand reputation and customer satisfaction. This automated approach is often more efficient and accurate than manual inspection, particularly for high-volume production lines.
Productivity and Efficiency
By identifying anomalies in production processes, manufacturers can pinpoint bottlenecks, optimize resource allocation, and improve overall efficiency. This can involve analyzing sensor data from production equipment to identify deviations from optimal operating parameters, tracking production metrics such as cycle times, throughput, and yield to identify inefficiencies, and monitoring worker performance to identify areas for improvement.
Anomaly detection can reveal hidden patterns and correlations in production data, providing valuable insights for process optimization and continuous improvement. For example, by detecting anomalies in machine performance, manufacturers can identify equipment that requires maintenance or adjustments, optimizing overall production efficiency.
Detecting Defects in the Manufacturing Process
Anomaly detection can be used to identify defects in the manufacturing process itself, such as deviations from standard operating procedures or equipment malfunctions. This enables proactive interventions to correct the process and prevent further defects.
By analyzing sensor data from various stages of the manufacturing process, anomaly detection algorithms can identify subtle deviations from established norms, indicating potential problems such as variations in temperature, pressure, or material flow. Early detection of these anomalies allows for timely corrective actions, preventing the production of defective products and minimizing waste. This proactive approach improves overall product quality and reduces the cost associated with rework or scrap.
Predictive Maintenance
Anomaly detection plays a crucial role in predictive maintenance by identifying subtle changes in equipment behavior that may indicate impending failures. This allows for timely maintenance interventions, preventing costly downtime and extending the lifespan of equipment.
By analyzing historical and real-time sensor data from equipment, anomaly detection algorithms can identify deviations from normal operating patterns, such as increased vibration, temperature fluctuations, or unusual power consumption. These anomalies can be early indicators of equipment degradation or impending failures. By detecting these subtle changes, manufacturers can proactively schedule maintenance activities, minimizing disruptions to production schedules and preventing catastrophic failures.
Minimize Safety Hazards
By detecting anomalies in safety-critical systems, manufacturers can identify potential hazards and take preventative measures to ensure worker safety. This can involve monitoring environmental conditions such as temperature, air quality, and noise levels, tracking worker behavior such as proximity to hazardous equipment or improper use of safety gear, and analyzing sensor data from safety systems such as fire alarms and emergency shut-off switches.
Anomaly detection can identify unusual patterns or deviations from established safety protocols, alerting personnel to potential hazards and enabling timely interventions to prevent accidents and injuries. This proactive approach to safety management enhances worker well-being and minimizes the risk of costly incidents.
Benefits of Anomaly Detection in Manufacturing
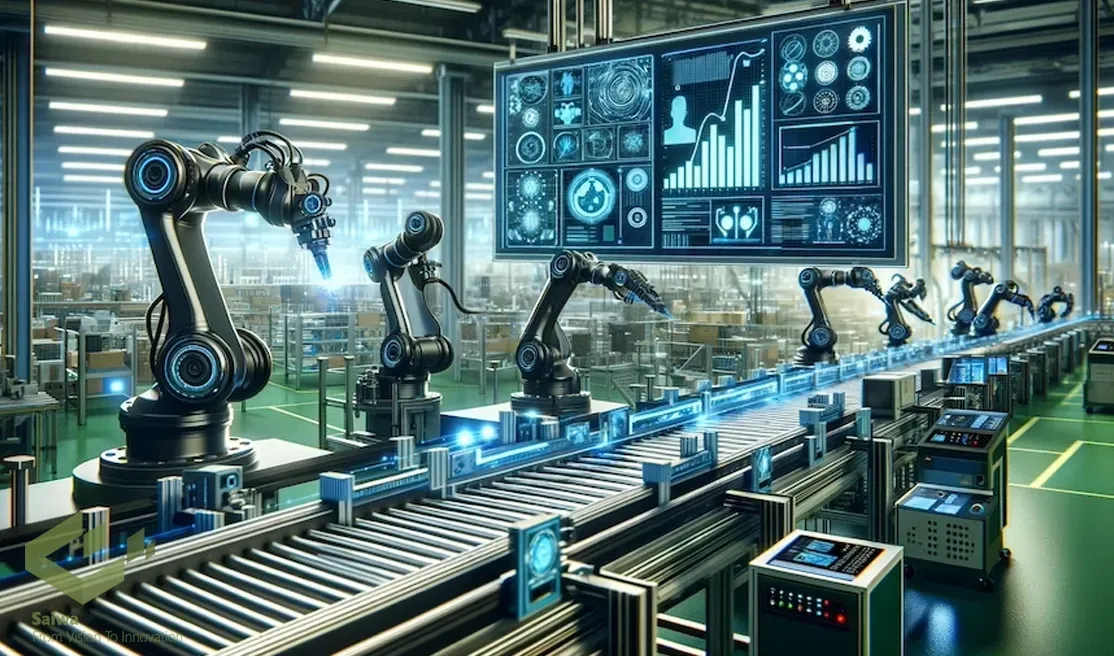
Implementing anomaly detection in manufacturing offers several benefits:
Data-Driven Insights
Anomaly detection provides valuable insights into manufacturing processes, enabling data-driven decision-making and continuous improvement. By identifying anomalies, manufacturers gain a deeper understanding of the factors that influence product quality, productivity, and safety.
These insights can be used to optimize processes, improve product design, and enhance decision-making across the organization. For example, analyzing anomalies in production data can reveal hidden correlations between process parameters and product quality, leading to more informed process adjustments and improved product consistency.
Improved Product Quality
By identifying and addressing defects early, anomaly detection improves product quality and reduces waste. Anomaly detection systems can automatically identify defects in real time, allowing manufacturers to quickly isolate defective products and prevent them from reaching customers.
This reduces the need for costly rework, scrap, and warranty claims, ultimately improving customer satisfaction and brand reputation. Furthermore, by identifying the root causes of defects, manufacturers can implement corrective actions to prevent similar defects from occurring in the future.
Increased Efficiency
Anomaly detection optimizes production processes, leading to increased efficiency and reduced costs. By identifying bottlenecks, inefficiencies, and deviations from optimal operating parameters, manufacturers can implement targeted improvements to streamline production processes and maximize resource utilization.
For example, anomaly detection can identify machines that are operating outside of their optimal parameters, allowing for timely adjustments or maintenance to prevent further performance degradation and optimize overall production efficiency.
Reduced Downtime
Predictive maintenance based on anomaly detection minimizes downtime and extends the lifespan of equipment. By identifying subtle changes in equipment behavior that may indicate impending failures, manufacturers can proactively schedule maintenance activities during planned downtime, minimizing disruptions to production schedules.
This proactive approach prevents costly unplanned downtime and extends the lifespan of equipment by preventing catastrophic failures and optimizing maintenance schedules.
Enhanced Safety
Anomaly detection enhances worker safety by identifying potential hazards and enabling proactive interventions. By monitoring various safety-critical parameters, such as environmental conditions, worker behavior, and safety system performance, anomaly detection systems can identify unusual patterns or deviations from established safety protocols.
These anomalies can serve as early warnings of potential hazards, allowing for timely interventions to prevent accidents and injuries. For example, detecting anomalies in worker proximity to hazardous equipment can trigger alerts, prompting immediate corrective actions to prevent accidents.
Cost Savings
By preventing failures, reducing waste, and optimizing processes, anomaly detection leads to significant cost savings. Reduced downtime minimizes lost production time and associated costs.
Improved product quality reduces the need for rework, scrap, and warranty claims. Increased efficiency optimizes resource utilization and reduces operational costs. Enhanced safety minimizes the risk of costly accidents and injuries. These combined cost savings contribute significantly to the bottom line.
Environmental Monitoring
Anomaly detection can be used to monitor environmental conditions in manufacturing facilities, ensuring compliance with regulations and minimizing environmental impact. By analyzing data from environmental sensors, anomaly detection systems can identify deviations from established environmental parameters, such as unusual emissions, temperature fluctuations, or changes in water quality.
These anomalies can indicate potential environmental problems, allowing for timely interventions to prevent pollution and ensure compliance with environmental regulations. This proactive approach to environmental management minimizes the environmental footprint of manufacturing operations and promotes sustainable practices.
Examples of anomaly detection in manufacturing
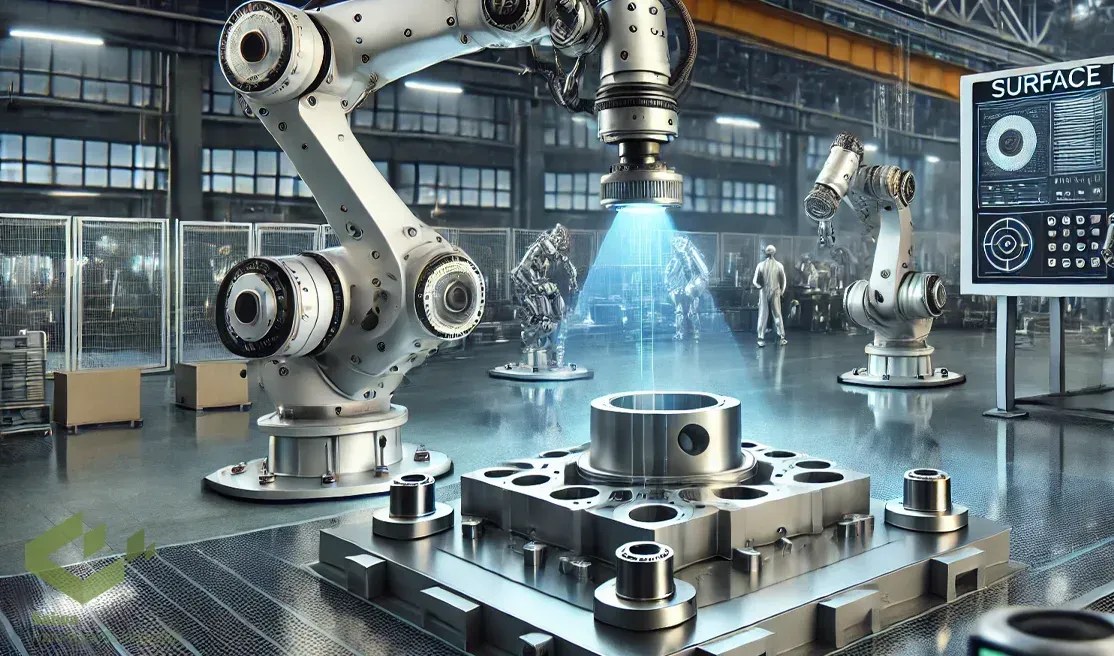
Surface Inspection in Metal Casting
Anomaly detection algorithms can analyze images of metal castings to identify surface defects such as cracks, porosity, or inclusions. These algorithms can be trained on large datasets of images of both acceptable and defective castings, learning to distinguish between normal surface variations and actual defects.
This automated inspection process can be significantly faster and more accurate than manual inspection, particularly for complex shapes and high-volume production. The early detection of surface defects allows for timely intervention, either by repairing the casting or rejecting it before further processing, minimizing waste and improving overall product quality.
Anomaly Detection in PCB Manufacturing
In printed circuit board (PCB) manufacturing, anomaly detection can be used to detect defects such as shorts, opens, or misalignments. Automated optical inspection (AOI) systems utilize anomaly detection algorithms to analyze images of PCBs, identifying deviations from the intended design.
These systems can detect subtle defects that might be missed by manual inspection, ensuring the reliability and functionality of the finished PCBs. Early detection of these defects prevents costly rework or scrap, and improves the overall quality and reliability of electronic devices.
Composite Material Inspection
Anomaly detection can be applied to inspect composite materials for defects such as delamination, voids, or fiber breakage. Techniques such as ultrasonic testing, thermography, or X-ray imaging can be used to collect data about the internal structure of composite materials.
Anomaly detection algorithms can then analyze this data to identify deviations from the expected material properties, indicating the presence of defects. This non-destructive testing approach allows for the early detection of defects, ensuring the structural integrity and performance of composite components in critical applications such as aerospace and automotive.
Glass Quality Control in Manufacturing
Anomaly detection algorithms can analyze images of glass products to identify defects such as scratches, bubbles, or cracks. These algorithms can be trained to recognize the characteristics of different types of defects, allowing for automated inspection and quality control.
This automated approach improves the efficiency and accuracy of glass inspection, ensuring that only high-quality products are shipped to customers. Early detection of defects minimizes waste and reduces the cost associated with rework or scrap.
Plastic Injection Molding Defect Detection
Anomaly detection can be used to detect defects in plastic injection molded parts, such as warpage, short shots, or sink marks. By analyzing sensor data from the injection molding machine, such as temperature, pressure, and flow rate, anomaly detection algorithms can identify deviations from normal operating parameters that may indicate the presence of defects.
This allows for real-time monitoring of the injection molding process and enables proactive interventions to correct process parameters and prevent further defects. This improves product quality and reduces waste associated with defective parts.
Anomaly Detection in Welded Joints
Anomaly detection algorithms can analyze images or sensor data from welded joints to identify defects such as cracks, porosity, or incomplete penetration. Techniques such as radiographic inspection, ultrasonic testing, or eddy current testing can be used to collect data about the internal structure of welded joints.
Anomaly detection algorithms can then analyze this data to identify deviations from the expected weld characteristics, indicating the presence of defects. This non-destructive testing approach ensures the structural integrity and reliability of welded joints in critical applications such as construction and manufacturing.
Rubber Quality Inspection
Anomaly detection can be used to assess the quality of rubber products by identifying defects such as cracks, blisters, or variations in thickness. This can involve analyzing images of rubber products, sensor data from testing equipment, or other relevant data sources.
Anomaly detection algorithms can be trained to recognize the characteristics of different types of defects, enabling automated inspection and quality control. This improves the efficiency and accuracy of rubber inspection, ensuring that only high-quality products are used in various applications.
CNC Machine Tool Monitoring
Anomaly detection can be used to monitor the performance of CNC machine tools, detecting anomalies that may indicate tool wear, misalignment, or other problems. By analyzing sensor data from the machine, such as vibration, temperature, and current, anomaly detection algorithms can identify deviations from normal operating patterns. These deviations can be early indicators of potential problems, allowing for proactive maintenance interventions to prevent costly downtime and extend the lifespan of the machine tools. This predictive maintenance approach optimizes machine performance and reduces maintenance costs.
Best Practices for Implementing Visual Anomaly Detection in Manufacturing
Successfully deploying visual anomaly detection in manufacturing requires more than just selecting an AI model, it demands a thoughtful approach to ensure accuracy, scalability, and long-term value. By following proven best practices, manufacturers can maximize the benefits of this technology and avoid common pitfalls.
Start with a Pilot Project: Begin by implementing visual anomaly detection in manufacturing on a single production line or product type. This allows you to evaluate performance, fine-tune the system, and build internal confidence before scaling across the facility.
Ensure High-Quality Data Collection: Capture images under various conditions, including different lighting and product variations. The success of visual anomaly detection in manufacturing depends heavily on the quality and diversity of the training dataset.
Combine AI with Human Expertise: Use a hybrid approach initially, where AI flags potential anomalies and human inspectors validate the results. This ensures accuracy while allowing the model to learn from expert feedback.
Monitor and Retrain Regularly: Production environments evolve over time. Periodically retrain the system with new data to maintain accuracy as materials, equipment, or processes change.
Optimize Camera Placement and Settings: Ensure consistent image capture by positioning cameras to minimize blind spots, glare, and shadows. Correct setup reduces false positives and improves detection rates.
Integrate with Existing Systems: Connect anomaly detection outputs with manufacturing execution systems (MES) or quality control workflows for faster decision-making and automated responses.
Adhering to these best practices ensures a smoother rollout, higher detection accuracy, and a sustainable return on investment for any manufacturing operation.
Future Trends in Anomaly Detection for Manufacturing
Several trends are shaping the future of anomaly detection in manufacturing:
Deep Learning Enhancements
Deep learning models, particularly Convolutional Neural Networks (CNNs) for image analysis and Recurrent Neural Networks (RNNs) for time-series data, are increasingly being used for anomaly detection due to their ability to handle complex data and identify subtle patterns. These models can automatically learn intricate features from raw data, eliminating the need for manual feature engineering. This allows deep learning algorithms to detect anomalies that might be missed by traditional methods, particularly in high-dimensional data sets common in manufacturing.
Furthermore, advancements in unsupervised and semi-supervised learning techniques are enabling deep learning models to be trained effectively even with limited labeled data, addressing a common challenge in manufacturing anomaly detection applications. This trend is leading to more accurate and robust anomaly detection systems, capable of handling the increasing complexity and volume of data generated in modern manufacturing environments.
Integration with Robotics
Anomaly detection is being integrated with robotics to enable automated inspection and repair of manufacturing equipment. This integration allows robots to not only identify anomalies through visual inspection, sensor data analysis, or a combination of both, but also to autonomously perform corrective actions. For example, a robot equipped with a vision system and anomaly detection software can identify a surface defect on a manufactured part and then automatically perform the necessary repairs or remove the defective part from the production line.
This integration of manufacturing anomaly detection and robotics increases automation in manufacturing, improves efficiency, and reduces the need for human intervention in potentially hazardous or repetitive tasks. This trend is driving towards smart factories where robots can autonomously monitor and maintain equipment, optimizing production processes and minimizing downtime.
Conclusion
Anomaly detection is a powerful tool that is revolutionizing the manufacturing industry. By identifying deviations from normal behavior, manufacturers can proactively address issues, improve product quality, optimize processes, and ensure safety. As technology continues to advance, anomaly detection techniques will become even more sophisticated, enabling manufacturers to extract valuable insights from vast amounts of data.
By leveraging AI, machine learning, and other advanced technologies, manufacturing anomaly detection systems can be developed to detect subtle anomalies that may be missed by human operators. This will lead to more accurate and timely identification of potential problems, reducing downtime, improving product quality, and increasing overall efficiency.
As the manufacturing industry embraces Industry 4.0 and the Internet of Things (IoT), anomaly detection will become an essential component of intelligent manufacturing systems. By harnessing the power of data and AI, manufacturers can drive innovation, improve productivity, and achieve sustainable growth in the years to come.
Note: Some visuals on this blog post were generated using AI tools.