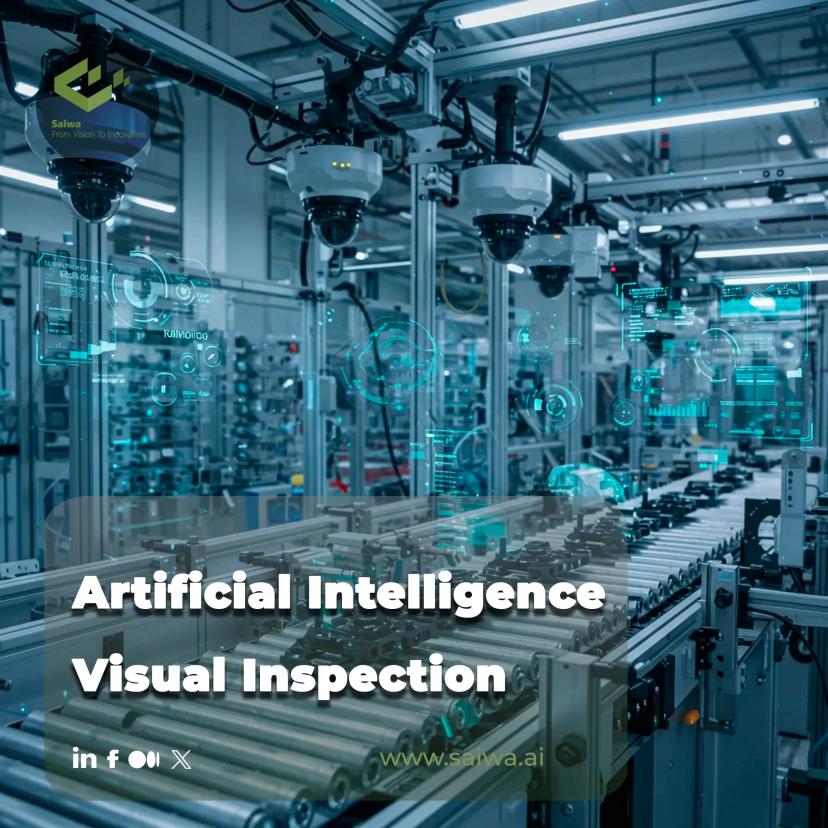
Artificial Intelligence Visual Inspection | Transforming Quality Control
Quality control is a key element of modern manufacturing and production processes across a wide range of industries. Traditionally, visual inspection, which relies heavily on human observation, has been the go-to method for ensuring product quality and identifying defects. However, human visual inspection is naturally prone to fatigue, subjectivity, and inconsistency, leading to potential errors and failures. The introduction of artificial intelligence (AI) offers a revolutionary solution that promises to alter quality control by automated visual inspection.
Fraime, developed by Saiwa, facilitates AI implementation across various industries, focusing on tools like surface defect detection for enhanced quality control in manufacturing. By identifying production anomalies early, Fraime helps manufacturers improve product quality, streamline workflows, and cut costs related to defects and reworks, all without requiring in-depth AI expertise internally.
This article explores the evolution of visual inspection, the invention and mechanics of AI-driven visual inspection, its benefits, applications, challenges, and future trends, ultimately highlighting its potential to reshape quality assurance patterns.
The Evolution of Visual Inspection in Manufacturing
Visual inspection has a long and growing history in manufacturing. At first, it relied solely on human "eyes" carefully inspecting products for defects. While this manual process was necessary, it was slow, labor-intensive, and prone to human error. As manufacturing became more automated, basic automated visual inspection systems were created that used simple sensors and cameras to detect major defects.
However, these systems lacked the finesse to identify subtle or complex defects. The increasing complexity of products and the demand for higher quality standards created the need for more advanced inspection techniques. This caused the integration of AI, allowing visual inspection systems to learn, adapt, and improve their accuracy over time.
Introduction of AI in Enhancing Inspection Processes
The shortcomings of traditional visual inspection methods, along with recent advancements in AI and computer vision, have led to the development of AI-powered visual inspection. AI algorithms, deep learning models in particular, can analyze complex visual data, identify detailed patterns, and make precise judgments about product quality.
This ability solves the problems that come with human inspection, reducing errors, improving consistency, and increasing the overall efficiency of inspections. AI-driven inspection systems can operate nonstop, which means they can be used 24/7. This significantly increases the production rate.
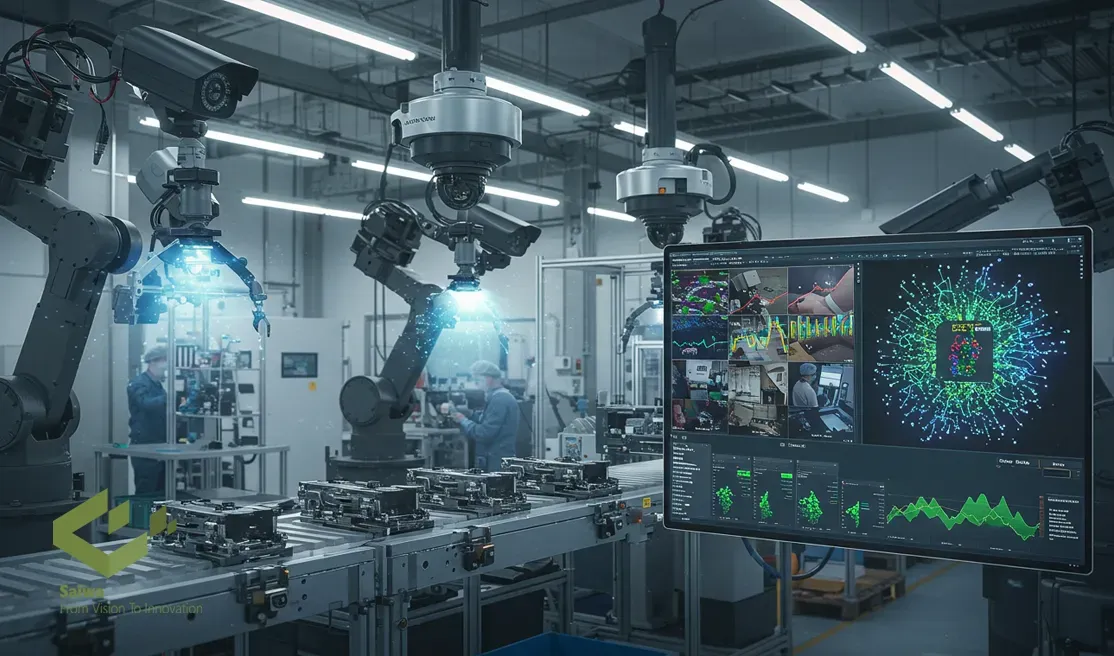
Defining AI Visual Inspection
AI visual inspection means using AI algorithms and computer vision techniques to automatically check products or parts for flaws. These systems use cameras and sensors to take pictures and videos of the items being checked. The visual data is then processed by AI algorithms that are designed to find different types of defects, like Surface defects detection, cracks, misalignments and other issues.
The system then marks these defects for further review or automatic rejection, making sure that only high-quality products get through the production line.
How AI Visual Inspection Works
AI visual inspection systems typically follow a process with several stages:
Image Acquisition
High-resolution cameras or sensors take pictures or videos of the product being inspected. These cameras can be placed in one of three ways: on a stand, on a robotic arm, or on machines that are already being used to make the product.
The process of image acquisition is adjusted to make sure that the lighting, focus, and perspective are always the same. This helps to make sure that the AI algorithms are always accurate. Sometimes, multiple cameras are used to take pictures from different angles and perspectives of the product.
Preprocessing
The collected images go through a series of steps to get preprocessed for the AI to use. These steps include noise reduction, image enhancements, and normalization to improve the quality of the input data for the AI algorithms. Noise reduction gets rid of unwanted artifacts or distortions in the pictures.
Enhancing contrast, brightness, and sharpness improves the quality of the images in the image enhancement step. Normalization standardizes the image data, making sure that all the images are consistent and improving the performance of the AI models. This step is very important to make sure that the later analysis is reliable and accurate.
Feature Extraction
AI algorithms, often based on deep learning models like convolutional neural networks (CNNs), find the relevant features from the images. These features stand for specific characteristics of the product, like texture, shape, color, and other visual qualities. CNNs are especially good at analyzing images because they can learn hierarchical representations of visual data . The features that are found are then used as input for the stage where defects are detected.
The specific features chosen and the design of the CNN are key factors in how well the system performs.
Defect Detection
The features that are found are compared to a pre-trained model of acceptable product characteristics. Any differences from this model are seen as possible defects. The pre-trained model is developed using a large set of images with labels, including both acceptable and defective products.
The comparison process involves calculating a similarity score between the features that are found and the features of the pre-trained model. A low similarity score means there is a possible defect. Complex statistical methods are used to set limits for detecting defects, reducing false positives and false negatives.
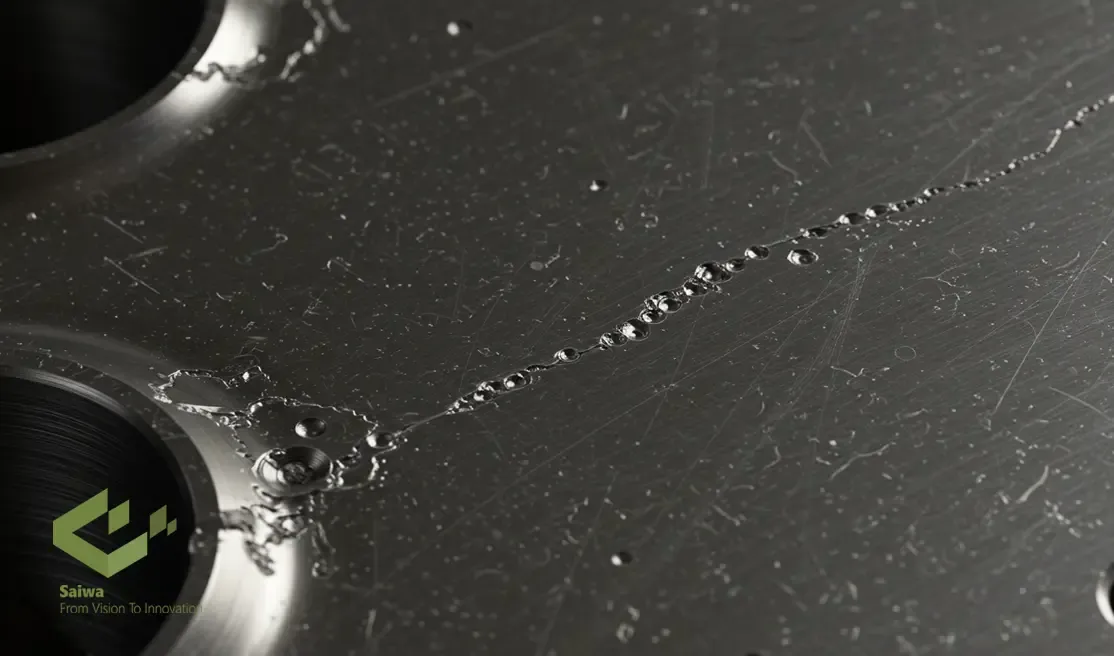
Classification and Localization
The system classifies the type of defect and finds its location on the product. The classification process involves putting the detected defect into a specific category, such as a scratch, crack, or discoloration.
The localization process figures out the exact location of the defect on the product, often using bounding boxes or segmentation masks. This information is necessary for guiding the next repair or rework processes.
Decision Making
Based on the defects detected, the system either rejects or accepts the quality of the product. This decision can be made automatically, or it can be made by a human operator reviewing the defects and making the final decision. The decision-making process can be adjusted based on the specific quality requirements of the product and the preferred level of automation.
Benefits of Using AI in Visual Inspection
Enhanced Accuracy and Consistency
AI visual inspection systems are more accurate and consistent than human inspection. AI algorithms are not influenced by personal biases or fatigue, leading to more reliable and repeatable inspection results. This increased accuracy reduces the risk of defective products reaching customers, improves brand reputation, and reduces warranty claims. Additionally, AI systems can detect subtle defects that might be missed by human inspectors, improving product quality and reducing risk. The consistency of AI-driven inspection keeps quality standards consistent in all products.
Increased Efficiency and Productivity
AI-powered inspection systems can inspect things a lot faster than human inspectors. This means more products can be made, and workers can focus on more complex tasks. AI systems can also work nonstop, which makes them more productive and reduces wasted time.
Cost Reduction
While AI visual inspection systems may cost more to set up, they can lead to big savings in the long run. These systems can reduce labor costs, minimize the amount of scrap and rework, and improve product quality, which can lower the overall cost of production. By detecting defects early in the production process, AI systems can reduce the cost of rework or scrapping defective products. Improved product quality also means fewer warranty claims and lower expenses.
Usability and Flexibility
AI-based inspection systems can be easily changed to fit different products and put into existing production lines. This makes them work well in many industries and for many uses. AI systems can handle more and more production volume without getting stuck on inspection quality. They can also be adjusted to check different types of products or adapt to changing production requirements.
Applications of AI Visual Inspection Across Industries
Manufacturing
Finding defects in manufactured parts, making sure that products are consistently high-quality, and checking for defects like Surface defects, cracks, and size problems in all kinds of parts. AI visual inspection can be used in many different manufacturing processes, like machining, casting, and molding.
Automotive
Checking car parts for flaws to ensure their safety and reliability. This includes checking important components like engines, brakes, and chassis for problems that could compromise vehicle safety. AI for quality control inspection can also be used in the process of putting together cars.
Electronics
Detecting defects in circuit boards and electronic components. This includes spotting problems with soldering defects, missing components, and other issues that could affect the functionality of electronic devices. AI visual inspection plays a crucial role in maintaining the quality and reliability of electronic products.
Pharmaceuticals
Inspecting pharmaceutical products for quality and integrity. The process includes checking the correct dosage, packaging integrity, and absence of contaminants in products. AI visual inspection helps ensure patient safety and compliance with strict rules and regulation requirements.
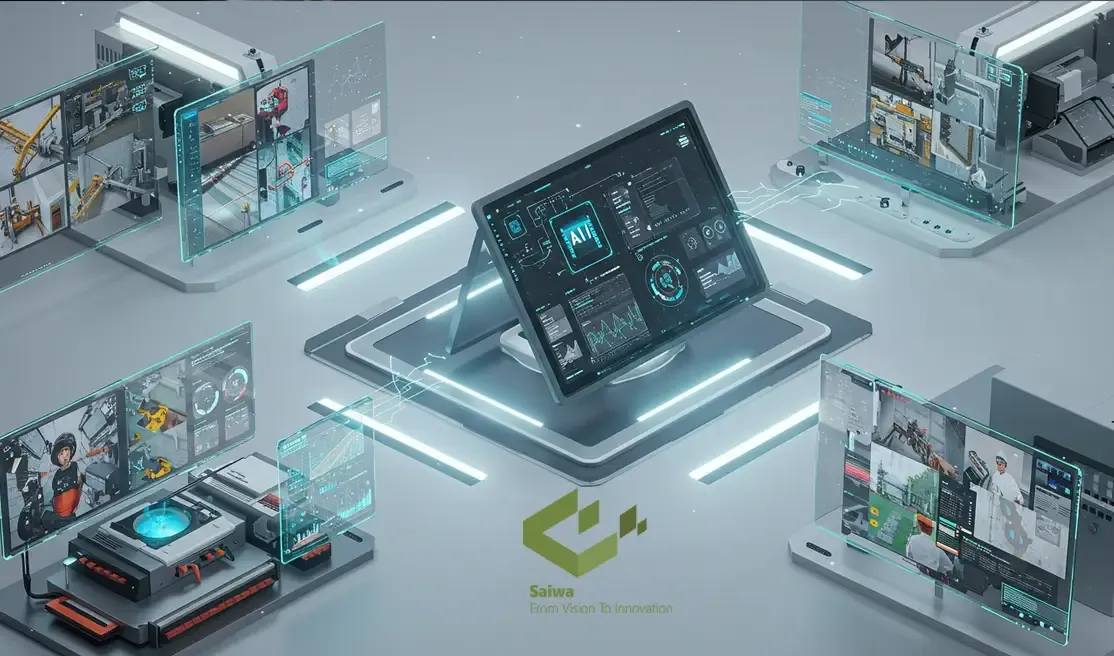
Challenges in Adopting AI Visual Inspection
High Initial Setup Costs
AI-based inspection systems require a lot of money to set up. You need to spend on hardware, software, and training. High-resolution cameras, special lighting equipment, and powerful computers can cost a lot in addition. Also, developing and training AI models requires expertise in machine learning and computer vision, further adding to the initial investment.
Data Requirements
AI algorithms require significant amounts of high-quality training data to perform best. Obtaining and labeling this data can take a lot of time and money. The quality of the training data directly affects how accurate and reliable the AI models are. Data augmentation techniques are used to increase the size and variety of the training dataset, but this can also add to the complexity and cost of development.
Adjusting to Existing Systems
Integrating AI visual inspection into an existing production line can be hard and require a lot of modifications to the current infrastructure. This may include integrating AI systems with automation and data management systems, as well as other production line equipment. Careful planning and execution are essential for a successful integration process.
Conclusion
AI visual inspection is going to completely alter quality control in many industries. By making the inspection process automatic, AI systems make it more accurate, efficient, and cost-effective, leading to high-quality products. While there are still challenges with the initial investment and data requirements, the long-term benefits of using AI visual inspection are worth it.
As AI technology continues to improve, we can expect even more advanced and powerful visual inspection systems that will completely change the way quality assurance works and shape the future of manufacturing and production.
Note: Some visuals on this blog post were generated using AI tools.