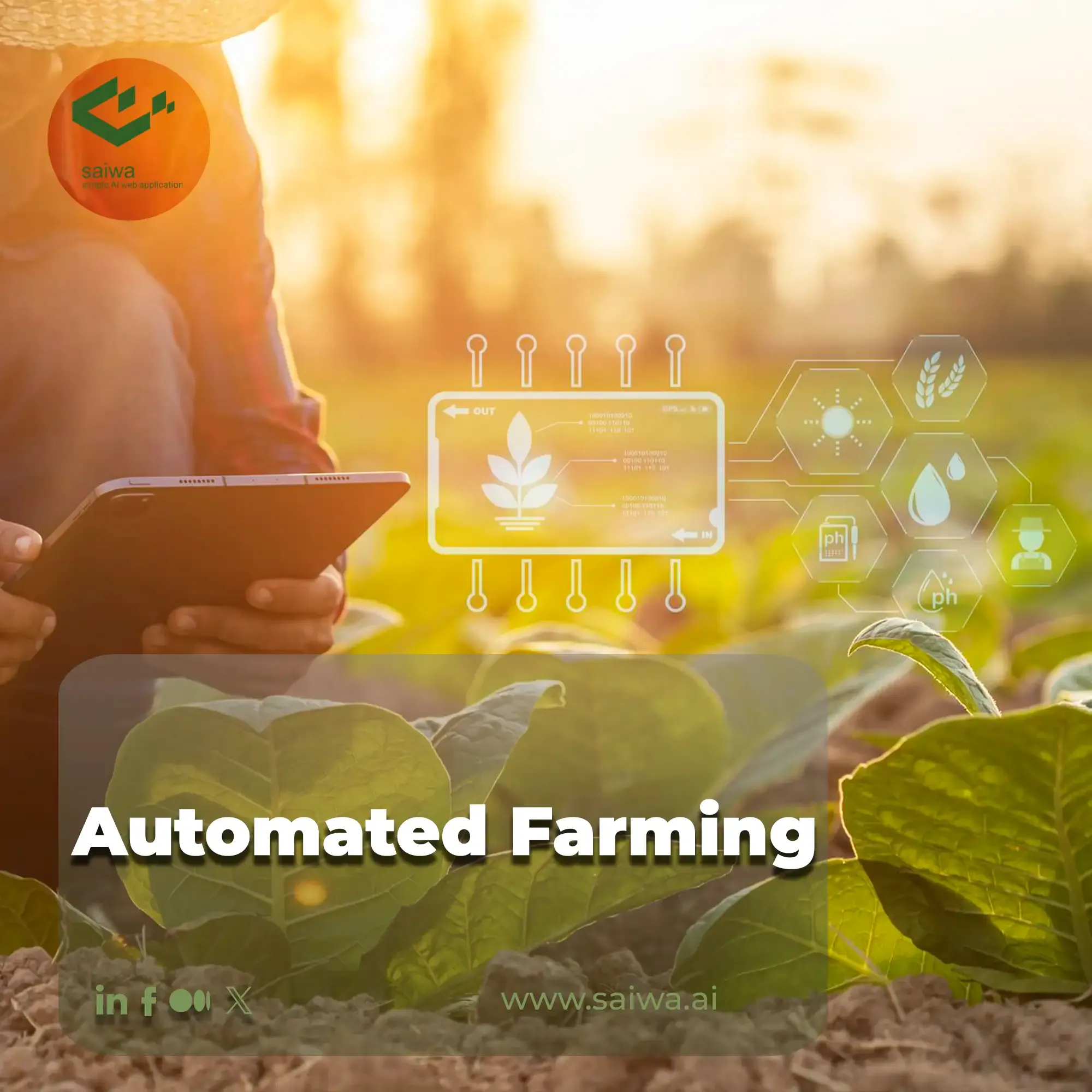
The process of farming development created a turning point for humans. Man's ability to engineer the environment to produce enough food to sustain massive population growth was the first major change in the relationship between fully modern humans and the environment. The advent of agriculture led to further advancements, including growing crops, cooking, self-driving cars, and more. Agriculture has been with humans for many years, but now we are living at its turning point. According to the forecasts that have been made, the production of farming products will also increase with the increase in population. The pressure on the farming industry to produce more crops puts more pressure on the health of the planet.
New technological developments in modern agriculture, from robotics and farming drones to computer vision software, have completely transformed modern agriculture. Farmers now have access to Automated farming tools that help them meet the demands of the world's ever-increasing population. In this blog, we decided to talk about Automated farming, its advantages, and challenges completely.
Read Also: AI in Agriculture | Practical Application & Future of AI in Agriculture
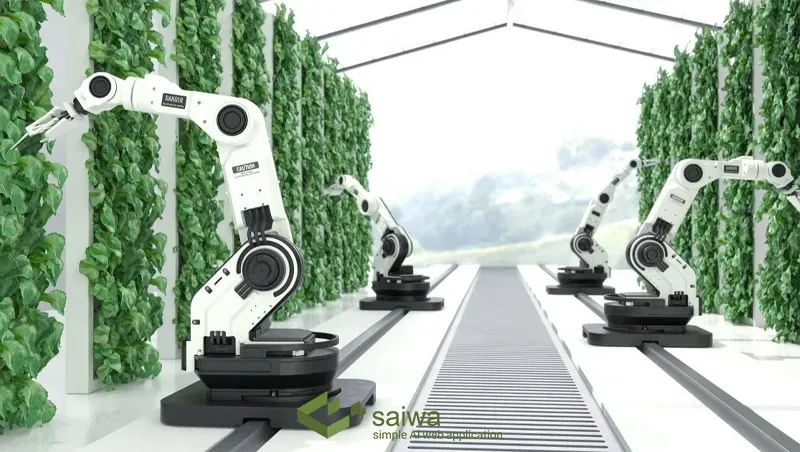
What is Automated Farming?
Automated farming, which is usually associated with smart agriculture, uses various technological devices to improve Automated farming operations and the crop or livestock production cycle and make farms more efficient. Most farming technology companies are now working on robotics innovations to develop drone operations, self-driving tractors, robotic harvesters, irrigation robots, and automated seeding. These technologies are indeed new, but the farming sector is witnessing an increase in the number of traditional farming companies that use farm automation in their processes.
Why is Automated Farming Important?
Few industries in modern society face the challenges seen in the farming sector. Many external forces wreak havoc on the farm business, and all of them are beyond the control of the business owner. Weather, drought, pests, and diseases permanently damage the farming industry.
They increase the standard risks that businesses face and put a lot of pressure on thin profit margins. As you progress through this, the list of challenges grows. If we imagine a farmer who has planted a certain number of seeds, he must also produce a number of products for his business to be viable. In the next step, the method of becoming more efficient and producing higher yields on the land is considered.
That is why farming automation has become important. Answers to questions such as how to increase your yield, how to harvest more, and how to reduce waste vary according to the type of farming.
How does Automated Farming work?
Automated farming is not only related to robots that can plant seeds and harvest crops; these technologies include automated planting, AI in soil management systems, and automated harvesting, as well as drones that monitor crops and provide data to farmers. They give. Automated agriculture includes advanced technologies such as robotics, sensor technology, satellite data, and mobile applications.
This type of farming uses less water because intelligent monitoring capabilities make it possible to know exactly when enough water has been delivered to a particular plant or field and the supply is cut off. Based on the same issue, a lower amount of drop killer will be used because no product is wasted for plants that do not grow well. Automated farming systems usually work on a 3-step mechanism:
Sensors and cameras monitor the products and detect any kind of problem
The software uses this data to make recommendations on the best way to manage the product
These recommendations are converted into actions by the machines themselves.
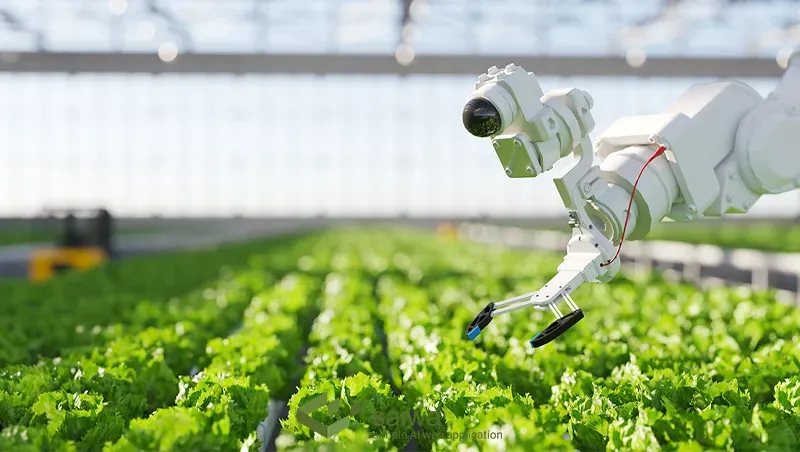
What technologies does Automated Farming Use?
The main goal of farming technology companies is to implement smart technologies to cover daily tasks. Some of the most famous technologies implemented in farms are:
Harvest Automation
Fruit and vegetable harvesting has often been challenging for farming automation. Harvesting robots should handle crops gently to avoid bruising and damage.Harvesting represents one of the most labor-intensive phases across agricultural operations. As labor shortages compound and farm sizes scale upwards globally, harvest automation processes offer invaluable efficiency improvements while addressing dwindling skilled worker availability. AI in automated harvesting provides capabilities surrounding computer vision, robotic motion control, and fleet orchestration that aim to replicate and even enhance the efficacies of human fruit pickers through sensors and algorithms.
When implemented astutely, AI-enabled autonomous crop harvesting solutions can deliver game-changing advancements over status quo manual methods including significantly boosting productivity per acre, ensuring the freshest and highest quality produce gets picked at ideal ripeness, while drastically cutting labor costs over manual harvest crews.
Autonomous tractors
Manufacturers can remotely control self-driving tractors or pre-program them to become autonomous.
Read Also: Find the Impact of AI in Self Driving Cars with our guide
Seeding and Weeding
Robotics designed for seeding and weeding can target specific crop areas. In seeding, they can reduce the day-to-day work of farming, while weeding robotics can reduce the use of herbicides by up to 90% with computer vision.
Read Also: An Over View Applications of Computer Vision in Agriculture
Drone
Farming drones can remotely monitor conditions and apply fertilizers, pesticides, and other treatments. Infrared images and analysis can quickly identify problem areas and help farmers spot problems early.
Read More: AI-Based Drone Operation| AI in Drones use cases
Guidance and Steering Technologies
The core technology enabling driverless functionality for tractors, harvesters, and other farm machinery is GPS guidance systems. GPS antennae and gyroscopic sensors feed location data to onboard computers connected to the steering axles and systems. This allows:
Autonomous steering to follow programmed routes through fields with extreme precision.
Planting/spraying/harvesting in perfectly straight lines to maximize efficiency.
Avoiding overlapping treatment areas or accidentally missing sections.
Reduced driver fatigue, distraction, and human error accidents.
These improvements in navigation precision, efficiency, and safety underlie most autonomous field equipment.
Sensors and Data Collection in Automated Farming Equipment
A range of nimble ground and aerial robots outfitted with different sensors produce valuable crop data:
- Aerial drones using visual, hyperspectral, and thermal cameras identify irrigation needs, diseases, yield rates, and other crop health clues throughout the season by scanning vast acreage from the sky.
- Ground robots equipped with probes to test soil chemistry, moisture sensors, and cameras create mapped field data models, informing irrigation, fertilizer, and pesticide applications tailored to micro-conditions.
- Passive monitoring systems track indicators like frost risk, wind damage, humidity, and equipment operations.
- Cloud-based data management platforms aggregate, analyze, and act on insights gathered autonomously in the field.
Read Also: Automated Agriculture Irrigation Systems
Robotic Harvesting Machines
For highly repetitive tasks like picking fruits and nuts, autonomous harvesting robots are gaining adoption. Vision systems, mapping, and robotic arms allow these machines to:
- Precisely navigate rows and trellises in orchards and vineyards.
- Identify ripe produce ready for picking via onboard cameras and sensors.
- Carefully grip and detach fruit with robotic limbs without bruising or damaging plants.
- Work around the clock in all weather without concerns of fatigue or productivity.
Freed from the limitations of manual harvesting, smart robotic harvesters boost yield rates and profit.
Computer Vision Systems for Harvest Automation
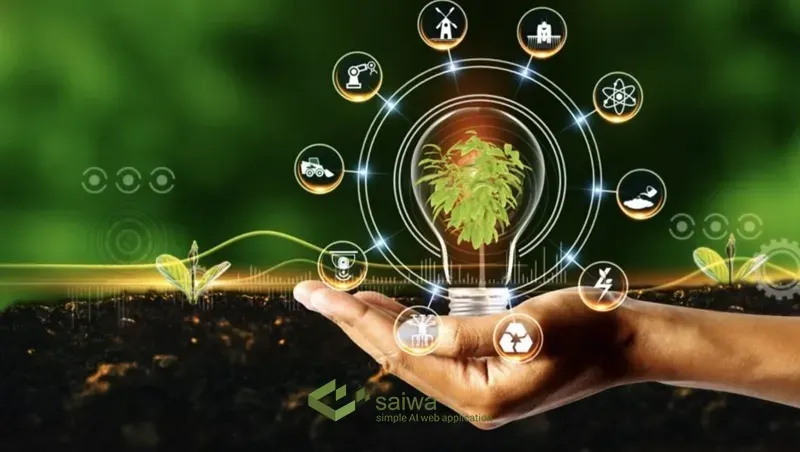
Sophisticated machine vision cameras and sensors play integral roles within harvest automation suited for specialty crops like tree fruits, citrus, and vegetables. Onboard cameras framed down crop rows continually scan plants assessing indicators of peak maturity including size dimensions, skin coloration shifts, and firmness.
Hyperspectral imaging detects exact spectra wavelength patterns across crops like apples or grapes to classify the level of sweetness and nutrient richness quantifying whether each fruit has achieved premium flavor suited for picking. Machine learning algorithms trained on sample crop image datasets programmatically tune sensitivity and specificity on these maturity triggers calibrated to specific apple strains for example being harvested to minimize premature picking while loss avoidance.
Obstruction Avoidance and Navigation
The same vision sensing also provides vital obstruction avoidance functionality allowing autonomous platforms to navigate fields safely without human assistance. 3D terrain maps localize bodies of water, and irrigation infrastructure above ground, and yield supporting structures to plot efficient routes avoiding collisions through narrow planting gaps.
With multiple robotic harvest automation operating as a fleet simultaneously, vision systems facilitate vehicle-to-vehicle positional awareness preventing conflicts. Integrated lidar sensors give proximity alerts to any foreign objects detected posing collision threats to trigger proximity alarms.
Quality Inspection and Sorting in Harvest Automation
Post-picking, inline quality inspection takes place by comparing each newly plucked item against ideal specimens with produce sorted accordingly. Minor defect identification ensures only premium grade produce moves forward minimizing unnecessary supply loss due to largely cosmetic damage. Robust onboard compute resources make real-time quality and maturity decisions without reliance on cloud connectivity.
Robotic Manipulator Arms
Specialized lightweight robotic arms mounted on autonomous harvester prototypes perform the crucial picking duties once crops slated for harvest are identified by the platforms’ computer vision scanning arrays. Gripper appendages get custom-engineered for the fruits gathered based on size, shape, and delicate skin sensitivity.
Pressure sensors determine the minimum grasping forces required to hold harvested materials steady through movements without causing bruising or penetration. Feedback camera guidance aids inappropriately picking trajectory motions tailored to that crop varietal.
Advanced Gripper Materials and Adaptive Design
For fruits like strawberries, polyurethane conformal foam lining gripper contact points adapt to delicate forms avoiding damage driven by rigid metal components. Adjustable tension settings prevent dropped materials from excessive compression or piercing skin integrity. Gripping multiple items per cycle boosts per-plant yield harvesting efficacies over single fruit grasp limitations common with emerging harvest robots.
Efficiency Boost through Multiple-Item Grasping
For collected items not passing onboard quality inspections, grippers reroute identified produce accordingly into alternate holding bins tagging reject materials for special handling compared to containers gathering premium output. Specialized anti-shock absorbing bin constructions prevent impact bruising over transport to sorting facilities. Some prototypes implement gentle shaking to allow reorientation of loaded items improving hauling density.
Fleet Coordination
Managing groups of independent autonomous picking robots across expansive orchards and fields introduces added complexity requiring orchestration software to direct vehicles efficiently. Harvest automation mission planners ingest readings for ground terrain accessibility, obstruction hazards noted from central data lakes, and crop maturity indicators from associated computer vision to assign prioritized sequences guiding the next locations each platform gets dispatched to for optimal fruit retrieval.
Dynamic Harvest Planning with Real-Time Ripeness Sensing
Updated ripeness sensing helps fine-tune collection plans daily as maturation shifts dictate which crop rows take immediate precedence for picking runs versus moving down pre-defined grid patterns oblivious of actual field conditions.
Optimizing Fleet Performance and Scalability
Continuous status monitoring tracks percentage completion across all harvester assets with overtime alerts flagging underperformers signaling potential maintenance to avoid prolonged downtime and schedule gaps. As fleets scale over successive seasons, simulations modeling yield variability histories and predicting future output volumes determine minimum projected fleet sizes required to complete tight seasonal harvest windows in the critical window ensuring produce gets picked at ideal states before spoiling Still Have Unused Capacity.
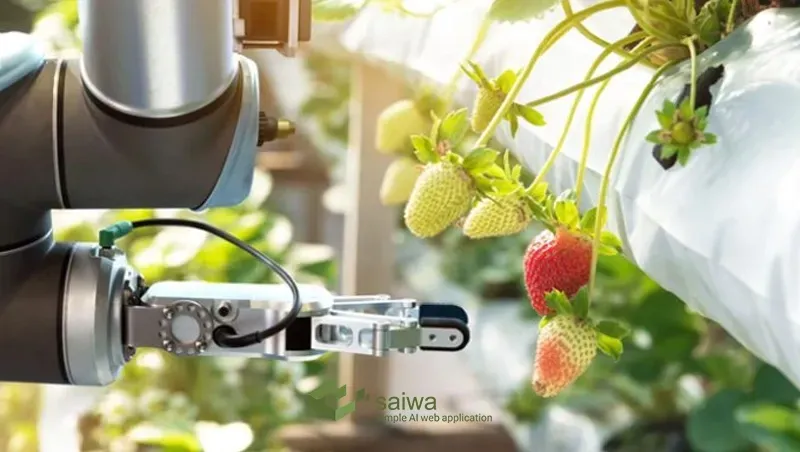
Supply Chain Transportation and Storage
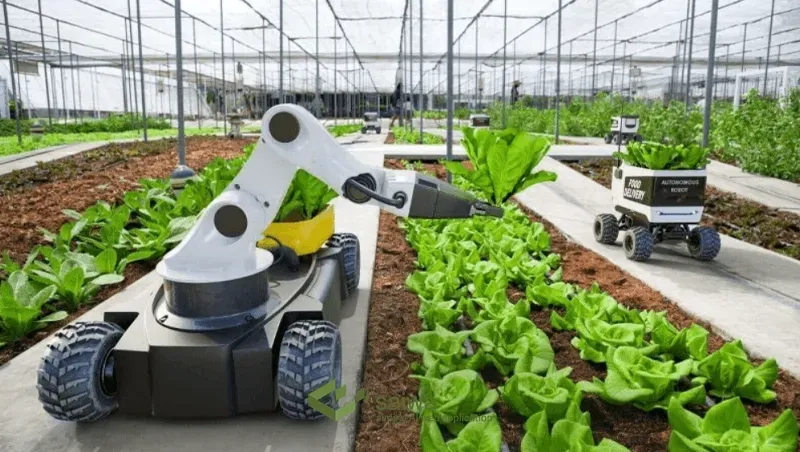
Post-harvest, maintaining food safety and quality becomes crucial. AI-driven telematics sensors monitor product environments during transit, triggering alerts when adverse conditions threaten shelf life. Connected analytics detect patterns correlated with higher levels of waste, enabling optimized transport protocols. Routing systems consider weather data, choosing routes less prone to delays, and ensuring perishables reach their destinations promptly.
Warehousing periods are enhanced with continuous air quality readings, allowing proactive climate control adjustments to preserve harvested materials. Advanced scanning technology ensures storage containers meet cleanliness requirements, preventing contamination. The result is a seamless and secure transition from harvest to distribution.
Read Also: A Deep Dive Into AI in Agricultural Supply Chain
The Specific Role of 5G and Edge Computing in Automated Farming
As automated farming technologies become more sophisticated, handling the immense flow of data and enabling split-second decisions becomes paramount. Traditional connectivity and processing methods can struggle with the demands of truly autonomous operations, especially those requiring intricate coordination like automated harvest systems. This is where the powerful combination of 5G wireless technology and edge computing steps in, acting as the digital backbone for the next generation of smart agriculture, enabling unprecedented levels of efficiency and responsiveness.
The Role of 5G
Fifth-generation (5G) wireless technology offers a leap forward with its ultra-low latency (minimal delay) and massive bandwidth capacity. For automated farming, this translates to the ability to transmit vast amounts of data from sensors, drones, and autonomous machinery in near real-time. This seamless communication is essential for coordinating fleets of robotic equipment, allowing instant adjustments based on live field conditions. Think of high-resolution video feeds from drones guiding ground robots or the intricate synchronization required for complex automated harvest systems operating across large areas – 5G provides the robust, high-speed network needed to make these scenarios reliable and effective.
The Power of Edge Computing
While 5G rapidly delivers the data, edge computing brings the processing power closer to where the action is happening. Instead of relying solely on sending data to distant cloud servers for analysis, edge computing performs critical calculations directly on or near the farm equipment. This drastically reduces response times for essential tasks, such as an autonomous tractor identifying and avoiding an unexpected obstacle or automated harvest systems making immediate micro-adjustments to gripping pressure based on fruit sensor readings.
Blockchain and Transparency in Automated Farming Systems
Blockchain technology is making significant strides in improving transparency and traceability within the agricultural sector, particularly in automated farming systems. As automated farming grows in complexity and usage, secure and transparent data management becomes more critical. Blockchain offers a decentralized ledger that ensures every transaction or data point is recorded, verified, and immutable. This provides a clear and traceable pathway from farm to consumer, enhancing trust and accountability in automated farming systems.
Key benefits of integrating blockchain with an automated farming system include:
Enhanced Traceability: Blockchain records every step of the farming process, from planting to harvesting. This helps in tracing the origins of products and verifying their authenticity, crucial for organic or fair-trade certifications.
Data Security: By providing a tamper-proof way of recording data, blockchain ensures that information regarding an automated farming system's operations, such as crop health and Crop Disease Detection, pesticide usage, and resource allocation, remains secure.
Improved Decision-Making: Farmers can make better decisions based on reliable and transparent data, optimizing resource usage and minimizing waste.
Consumer Trust: Blockchain allows consumers to access verified data about how their food was produced, fostering trust in automated farming systems and sustainable practices.
By merging blockchain with automated farming systems, the agriculture industry can move towards a more transparent, efficient, and sustainable future.
Beyond Crops: The Rise of Automation in Livestock Management
Despite the focus on crop production in many discussions about automated farming, parallel advances are changing the way livestock are managed. Often termed Precision Livestock Farming, this field uses technology to improve animal health, optimize productivity, and increase efficiency on farms raising animals. It's a vital component of the broader automated farming ecosystem.
Several key technologies are driving this shift:
Robotic Milking Systems: Advanced milking systems allow cows to choose when they are milked. These sophisticated robots handle the entire process automatically, simultaneously collecting valuable data on milk yield, quality, and individual animal health indicators without constant human supervision.
Automated Feeding Systems: These systems precisely dispense customized feed rations based on the specific needs of individual animals or groups. This ensures optimal nutrition tailored to each animal, minimizes feed waste, and significantly reduces the manual labor traditionally associated with feeding routines.
Sensor-Based Health Monitoring: Wearable sensors, often integrated into ear tags or collars, continuously track activity levels, rumination patterns, body temperature, and other vital signs. Analyzing this data helps farmers detect potential illness or key reproductive events much earlier than relying solely on traditional observation methods.
Automated Environmental Control: Technology now manages barn environments more effectively. Automated systems adjust ventilation, temperature, humidity, and lighting to maintain optimal conditions for animal welfare, comfort, and growth, adapting dynamically to changing needs.
By integrating automated farming tools into livestock management, farmers can access vast amount of data which help them in decision-making process and enhance both animal well-being and farm profitability within the expanding world of automated farming.
Vertical Farming and Urban Agriculture
While automated farming is often associated with vast fields and rolling tractors, a new wave of innovation is taking root in the heart of cities: vertical farming. These indoor, multi-layered greenhouses leverage automated farming to cultivate crops in urban environments.
Vertical farms are stacked ecosystems, maximizing space with automated farming systems for lighting, irrigation, and climate control. Automated seeding and harvesting robots ensure efficient production, minimizing human labor and maximizing yield. This allows fresh, local produce to be grown year-round, regardless of weather conditions, right within city limits.
The benefits of this future of urban farming revolution are numerous. Vertical automated farming reduces transportation costs and emissions associated with traditional farming. By using automated monitoring and resource management, they minimize water waste and create a more sustainable growing environment. Consumers enjoy fresher, locally-grown produce with a reduced environmental footprint.
However, challenges remain. The initial investment for setting up a vertical farm with its automated farming systems can be significant. Optimizing energy consumption and ensuring the long-term viability of these systems requires ongoing research and development. Despite these hurdles, vertical farming with its automated farming processes presents a compelling vision for the future. By integrating automation throughout the growing process, vertical farms offer a glimpse into a future where fresh, sustainable food production thrives in the heart of our cities.
Read Also: AI in Vertical Farming | The future of crop production
Advantages of Automated Farming
Automated farming addresses important issues such as global population growth, farm labor shortages, and changing consumer preferences. The advantages of automating traditional farming processes are many, but in this section, we want to focus on the most important advantages:
Consumer benefit
Consumer preferences towards organic and sustainable products are changing. With the help of Automated farming, products will reach consumers faster, fresher, and more sustainable. Increasing productivity from automation increases efficiency and production rate and thus reduces consumer costs. Additionally, the enhanced traceability of farm automation ensures that consumers have greater transparency regarding the origin and quality of their food, building trust and satisfaction. Farm automation also allows farmers to reallocate labor to more complex tasks that require human expertise, enhancing overall productivity. As a result, farms can operate more efficiently even with smaller workforces, addressing the growing challenges of labor shortages.
Labor productivity
Labor constitutes more than 50% of the costs of growing farms; half of the farmers say that the lack of labor affects them, that's why most of them go to low-labor products. However, there is vast potential for machine learning to harvest. Routine tasks can be automated with robotic technology, reducing labor costs in the farming industry. Farm automation also allows farmers to reallocate labor to more complex tasks that require human expertise, enhancing overall productivity. As a result, farms can operate more efficiently even with smaller workforces, addressing the growing challenges of labor shortages.
Read more: The impact of Machine learning in agriculture
Reduced Environmental Footprint
Automated farming can make the farming process more profitable and sustainable at the same time. By implementing precision agriculture techniques, farmers can selectively reduce their environmental footprint through pesticides and fertilizers and reduce chemicals in the soil and surrounding waterways. Also, automated systems can greatly help farmers save energy and water and reduce environmental impacts.
Boosts Efficiency
Automated farming equipment like GPS-guided tractors and robotic harvesters work with optimized precision unmatched by humans. These machines can operate continuously without breaks, covering more ground in less time and ensuring consistent quality. By minimizing human error and maximizing the precision of tasks such as planting and harvesting, farm automation significantly reduces waste and enhances overall productivity. The ability to fine-tune operations in real time also allows farmers to adapt quickly to changing conditions, ensuring optimal performance throughout the farming season.
Provides 24/7 Reliability
Farm robots continue tasks reliably regardless of weather, fatigue, light conditions or other variables that restrict human work. They can be programmed to operate around the clock, ensuring that critical farming activities are performed on time. This continuous operation not only increases output but also allows for better scheduling and management of resources, leading to a more resilient farming process. As a result, farmers can maintain consistent production levels even during peak seasons or unexpected challenges by farm automation
Generates Valuable Data
Onboard sensors in automated farming equipment collect vast data to reveal insights and inform enhanced practices. This data can be analyzed in real-time to detect early signs of crop stress, soil deficiencies, or pest infestations, enabling proactive intervention. Over time, the accumulation of data creates a rich resource for predictive analytics, helping farmers make more informed decisions and improve long-term yields. Additionally, data-driven insights from farm automation can be shared across the agricultural community, contributing to broader advancements in farming practices.
Enhances Profitability
Although automated farming equipment requires an upfront investment, reducing long-term labor costs improves overall farm profit margins. Driven by these advantages, farms of all sizes are adopting smart machines tailored to their needs and crops. As farm automation evolves, the return on investment is expected to grow, making automated farming a financially viable option for farms of all sizes. The cumulative financial benefits also position farmers to reinvest in their operations, driving continuous improvement and innovation.
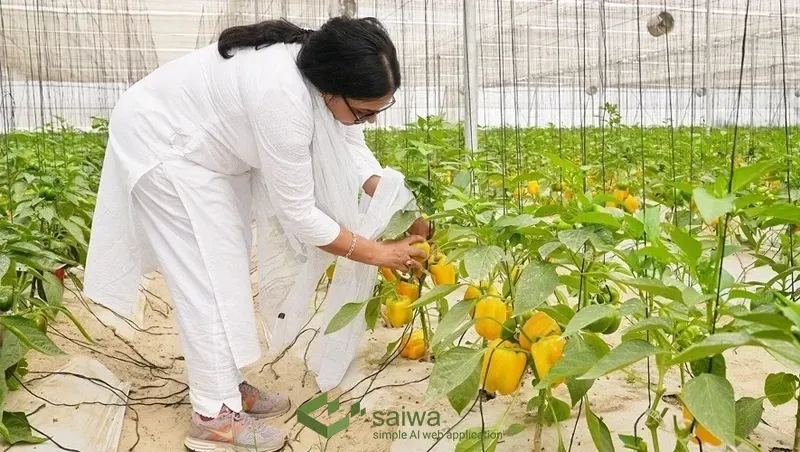
Challenges of Automated Farming
Of course, it must be said that there are currently challenges to overcome in this field. High costs for adopting robotic technologies can be a big barrier for farmers to enter, especially in developing countries. Technical problems and equipment failure can also cause high costs for the repair of this specialized automated farming equipment. Farmers must combine their knowledge and experience with these new technologies to take full advantage of farm automation.
Why aren't Farmers Adopting Automated Farming Faster?
Despite the many benefits of automated machines, why aren't more farmers looking to robots to help them and make life easier? Well, there are several reasons why farming processes have not been automated before:
First of all, it should be said that automatic machines are a little more complicated than an old tractor, and this requires experts to teach farmers how to use machines. Constant maintenance also requires a specialist, something that a farmer or some wrenches and grease are unlikely to fix.
Second, most machines are specialized because they are designed to do only one task, but humans are a little more adaptable. For example, you cannot use an automatic tomato picker to pick strawberries. This means that farmers have to invest more money to buy a large number of specialized automatic farming machines.
The third issue is the cost. Compared to traditional farming equipment, new automatic machines are more expensive.
Impact of Automated Farming on Rural Economies
The adoption of automated farming technologies is reshaping rural economies, offering both opportunities and challenges.
Economic Growth: Automated farming significantly boosts agricultural productivity, enabling farmers to cultivate greater quantities of crops in a shorter period of time. This leads to an increase in local exports and stimulates economic growth in rural areas.
Job Creation and Transformation: While automation reduces the necessity for traditional manual labor, it creates demand for skilled professionals to manage, maintain, and innovate automated systems. This transformation offers new job opportunities for rural workers, particularly in technology and engineering.
Cost Reduction for Farmers: The optimization of resources, including water, fertilizers, and seeds, enables automated farming to assist farmers in reducing operational costs. The precision of automation eliminates inefficiencies, making farming more profitable in the long run.
Empowerment of Small Farmers: Although initial investments in automation may be considerable, the availability of subsidies and shared equipment models allows small-scale farmers to benefit from advanced technologies. This inclusion helps reduce disparities within the rural economy.
Market Competitiveness: Farmers who adopt automated farming techniques can meet market demands more effectively, ensuring consistent quality and quantity of produce. This enhanced competitiveness serves to reinforce the economic viability of rural agricultural enterprises in comparison to their urban counterparts.
Infrastructure Development: The implementation of automated farming necessitates improved infrastructure such as better internet connectivity, storage facilities, and supply chains, indirectly benefiting rural development.
Ethical Considerations and Sustainability in Automated Farming Systems
The adoption of automated farming systems technology raises important ethical considerations related to environmental sustainability, food security, and social responsibility. While these technologies offer potential benefits in terms of resource efficiency and productivity, their impact on ecosystems, biodiversity, and rural communities must be carefully evaluated.
One key ethical concern in automated farming systems is the potential for increased monoculture cultivation and the associated risks of biodiversity loss, soil degradation, and vulnerability to pests and diseases. Automated farming systems practices should be designed and implemented in a way that promotes agricultural diversity, soil health, and ecosystem resilience. Additionally, the socioeconomic impacts of automated farming systems on rural communities and the agricultural workforce must be considered.
Strategies for reskilling and job transitions may be necessary to mitigate potential job displacement and ensure that the benefits of automated farming] are distributed equitably across society.
Regulatory Frameworks and Policies for Automated Farming Systems
The rapid development and adoption of automated farming systems technology have highlighted the need for appropriate regulatory frameworks and policies to ensure responsible and sustainable implementation. Government agencies and policymakers play a crucial role in establishing guidelines and standards for the use of these technologies.
Regulations may address issues such as data privacy and security, automated farming equipment safety standards, environmental impact assessments, and ethical guidelines for the development and deployment of automated farming technologies. Additionally, policies may be needed to incentivize the adoption of sustainable and responsible practices in automated farming systems.
The Future of Automation in Agriculture
Imagine a scenario where tractors can drive themselves, gentle robots harvest crops and drones snap with data about the health status of plants. This is not fiction but an introduction to the dynamic world of agriculture. Automation in agriculture is transforming the way we grow food, promising a future that's both productive and sustainable.
Automated Workflows: Think about self-driven tractors moving along fields with robotic arms softly harvesting crops while real-time data are being collected by drones on how plants are doing. This is the future envisioned by automation in agriculture.
Efficiency Boost: Repetitive tasks like planting, weeding, and harvesting will be automated, freeing up farmers' valuable time and resources. This allows them to focus on strategic planning, market trends, and the overall management of their farms.
Sustainable Solutions: Data-driven automation will lead to a sustainable agriculture solutions. Sensors and advanced analysis will allow for precise application of water, fertilizers, and pesticides. This minimizes waste and reduces the environmental footprint of farming practices.
Feeding the Future: Automation in agriculture has the potential to address the growing global food crisis. By increasing yields and reducing reliance on manual labor, we can ensure food security for future generations.
However, the transition to Automation in agriculture requires careful consideration. Equipping farmers with the necessary skills to operate and maintain these new systems is crucial. Additionally, ensuring the affordability of automation technology for both small and large farms will be essential for inclusive growth in the agricultural sector.
The future of Automation in agriculture is undeniably automated. By embracing these advancements, we can cultivate a more productive, sustainable, and food-secure future for all.
Conclusion
We are indeed in the early stages of automated farming, but when we look to the future, it is clear that automation will play an important role in the farming industry. With the help of technological advances, the farming process becomes more complex every year, and what was more advanced a few years ago will soon become standard and affordable. In addition to being useful for farmers, this work is also good for the environment. In addition to increasing productivity and reducing costs, automated farming has the potential to make agriculture a safer and more sustainable industry. The human element is always important for conflict management, but automated farming is essential for human survival.